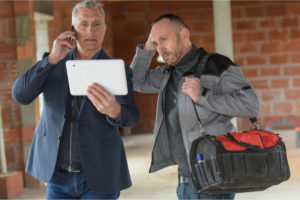
You have been watching the roller-coaster ride lumber prices have been on here, here, and here. But logs and lumber aren’t the only commodities that have been taking a wild ride on inflation. Prices for everything from copper, brass, and tin to PVC pipe have been unpredictable since the COVID-19 housing boom began in “Zoom towns.”
The chaos of 2020 exposed the madness of living in big cities, and now Americans are looking for their own paradise in the country, which means building houses and using lots of commodities to do it.
Add to the press for more building materials a Fed and federal government that seem hell-bent on generating inflation, and construction companies are being forced to navigate a storm of rapidly changing materials prices. Bob Tita reports in The Wall Street Journal:
Construction companies, manufacturers and other businesses that submit bids to win jobs say that process has turned unpredictable as rising materials costs expose them to potential losses.
As projects and orders stack up in a rebounding U.S. economy, some construction and manufacturing executives said they are surrendering profits on jobs or paying out of their own wallets to cover materials costs that exceed their bids.
Rising prices for steel, copper, brass, lumber, laminate sheeting and plastic-based materials, such as PVC pipe, are particularly hard to predict and factor into bids, according to executives. Inventories of materials remain tight because of production and transportation bottlenecks as well as growing demand. That has juiced some prices to record levels, including the U.S. spot-market price for coiled sheet steel, which has increased by more than 80% since the start of the year.
At Harper Construction Co., a San Diego-based construction contractor specializing in projects funded by the federal government, its president, Jeff Harper, said he has shelled out about $2 million this year to cover materials costs that exceeded his bids.
“It’s a real gamble,” Mr. Harper said. “It’s tough right now to figure out how to get work against a dozen competitors and not lose your tail in the process.”
Mr. Harper’s company constructs office buildings and other structures for federal agencies and the military. He said federal contracts typically have no provisions for contractors to recover higher costs for materials once a bid is accepted.
For manufacturers and builders, months can pass between the time bids are submitted and when the actual work begins. In the past, materials suppliers typically guaranteed prices for 60 to 90 days and often stuck to those prices if orders came in later than that, executives said. Now suppliers are quoting prices for just a week or two, and many aren’t honoring them beyond that, as prices steadily climb.
“Right now, I’m not giving any quotes on steel that I don’t own or am real confident of owning in the next 45 days,” said Lisa Goldenberg, president of Delaware Steel Co., a distributor near Philadelphia.
As a result, executives said they are doing more estimating on materials expenses than ever before. That can be risky when prices are rising. Companies that build in too many price increases into their bids can be easily underbid by competitors who don’t. Underestimating exposes building and manufacturing companies later on to higher costs, which their customers are often unwilling to cover once a contract is signed.
Action Line: If you want to escape the city, instead of building your dream mansion right away, maybe take some time to live small, cheap, and safe in America.